
Other Machinery
Singapore’s advanced manufacturing sector is witnessing rapid growth, with demand for high-quality precision engineering solutions rising across industries such as aerospace, electronics, semiconductors, and medical devices. As a leader in precision sheet metal fabrication and laser machinery, Sg Laser has solidified its position as a market leader by delivering superior craftsmanship, cutting-edge technology, and unparalleled customer service.
With a commitment to high-quality manufacturing, advanced automation, and stringent quality control, our machines deliver exceptional accuracy and productivity, meeting the demands of modern industries. Trusted by electrical manufacturers and industrial professionals, SG Laser is your go-to partner for cutting-edge solutions that drive efficiency and excellence.
.png)

Precision and Accuracy
High Efficiency
Reduced Waste
PRECISION BUS-BAR PUNCHING MACHINE
A CNC (Computer Numerical Control) Bus-bar Punching Machine is an advanced piece of equipment used for punching holes, slots, or other shapes into bus bars. These bus bars are typically made of copper or aluminum and are essential components in electrical distribution systems, where they conduct electricity within electrical panels, switchgear, and power distribution units.
A CNC Bus-bar Punching Machine utilizes CNC technology to automate the punching process, ensuring precise and consistent results with high production efficiency. Below is a detailed explanation of its components, working principle, advantages, and applications:
Atomation
-
CNC technology ensures that every hole is placed exactly where it is needed with high precision. This is critical for electrical systems where exact fit and performance are required
-
With the ability to punch multiple bus bars quickly, CNC punching machines greatly increase production rates compared to manual punching.
-
The machine’s automated processes reduce the need for manual labor and human error, improving consistency and speed.
Customizability
-
The CNC control system allows for a wide range of hole sizes, spacing, and patterns, offering flexibility in bus bar customization
Integration with Other Processes
-
Some models can integrate punching, bending, and cutting operations into one machine, further increasing production efficiency.
-
Due to precise control over hole placement and punching force, there is less material waste and a more efficient production process.
The primary purpose of a CNC Bus-bar Punching Machine is to punch holes, slots, or various shapes into bus bars, typically for electrical installations. It helps in preparing the bus bars for connections, mounting, and proper fitting into electrical panels or systems.
The CNC Bus-bar Punching Machine works by automatically following pre-programmed instructions to punch holes or shapes in the bus bars. Here's an outline of how it works:
Operation Process:
-
Programming: The operator programs the punching pattern into the CNC control system. This could include the size, number, and placement of holes, slots, or any other features required.
-
Feeding: The bus bar is placed on the machine bed or conveyor. The feeding mechanism automatically moves the bar into position for punching.
-
Punching: The hydraulic or pneumatic punching mechanism applies force to the punch tool, creating the desired hole or shape in the bus bar. The machine automatically moves the bus bar between punches, ensuring accuracy in hole spacing and alignment.
-
Ejection: Once the punching process is complete, the bus bar is either ejected manually or automatically for further processing or use.
A CNC Bus-bar Punching Machine is a modern, high-precision tool used to punch holes, slots, or other shapes into bus bars used in electrical systems. By leveraging CNC technology, these machines ensure high accuracy, speed, and flexibility in manufacturing bus bars for power distribution panels, switchgear, and other electrical systems. They offer major advantages such as automation, reduced labor costs, precision, and the ability to work with different materials and designs.
Summmary:
Advantages of CNC Bus-bar Punching Machine:
CNC Bus-Bar Bending Machine
A bus-bar bending machine is a piece of industrial equipment used to bend copper or aluminum bus bars, which are conductors used to distribute electrical power in various electrical systems. These bus bars typically come in flat, rectangular, or round edge, and they need to be bent to fit into electrical panels, switchgear, or other equipment enclosures. The bending process ensures that the bus bars conform to the specific design of the electrical system.
The breakdown of how a bus-bar bending machine works is being discussed below.
Purpose:
The primary function of the bus-bar bending machine is to bend bus bars with precision and accuracy, so they fit correctly in electrical panels, power distribution units, switchgear systems, or other electrical assemblies.
Advantages of Using Bus-bar Bending Machine:
Precision
Time-Saving
-
Ensures exact bending angle accuracy according to design specifications.
-
Speeds up the bending process.
Consistent Quality
Versatility
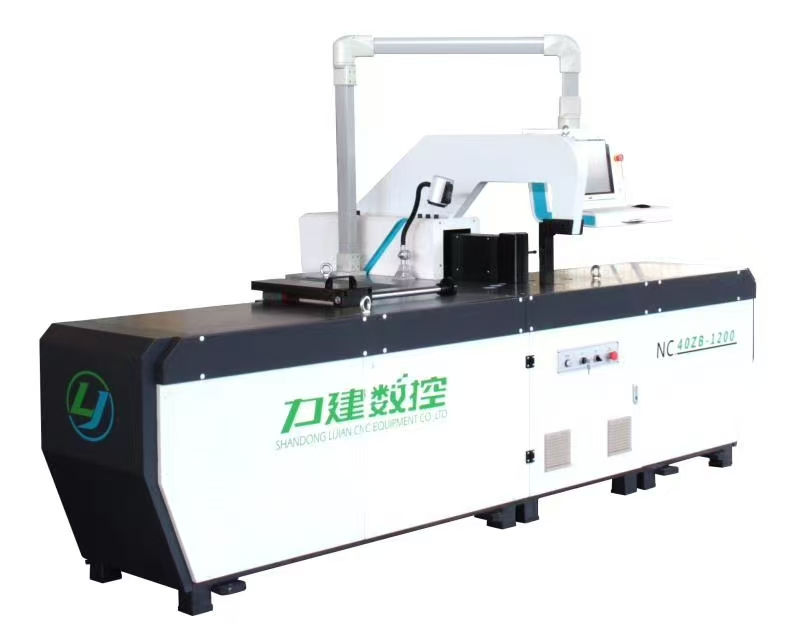
-
Helps in achieving uniform bends & accuracy across multiple bus bars.
-
Can accommodate various sizes of bus bars and bending angles, depending on the machine model.
Summary:
These machines are equipped with advanced controls and can automatically bend bus bars to precise specifications without much manual intervention. They are often used for high-volume production and offer the highest level of precision and consistency. In summary, a bus-bar bending machine simplifies and automates the process of shaping bus bars for use in electrical systems, ensuring efficiency, precision, and consistency.
CABLE STRIPPING MACHINE
A cable stripping machine is an industrial tool used to remove the outer insulation and sheathing from electrical cables, leaving the internal wires exposed. These machines are widely used in the electrical, electronics, and recycling industries to prepare cables for further processing, such as terminating, soldering, or recycling.
Purpose:
The main function of a cable stripping machine is to strip off the outer layer (insulation) of cables, which could be made from various materials such as rubber, plastic, or other polymers. This enables the exposed copper or aluminum wires inside to be used in electrical connections, repairs, or recycling.
Cable Stripping Machines by SG Laser Offers the Following Advantages:


Efficiency:
-
Cable stripping machines significantly speed up the stripping process, especially for large volumes of cables.
-
Automated models reduce the need for manual labor and ensure consistent quality.
Versatility:
-
Many machines can handle various cable sizes, insulation types, and wire gauges, making them adaptable for different tasks.
Safety:
-
Reduces the need for manual stripping, which can be time-consuming and dangerous if done improperly. The machine’s automated process reduces worker exposure to sharp objects and
Precision:
-
These machines provide consistent, accurate stripping lengths and minimal damage to the internal wires, which is critical for electrical connections.
Cost-Effective:
-
While the initial investment may be high, cable stripping machines can reduce labor costs and increase output, making them cost-effective in the long run.
Summary:
A cable stripping machine is a valuable tool in any industry that deals with electrical cables. By providing precise, automated, and efficient stripping of cable insulation, these machines increase productivity, reduce manual labor, and ensure high-quality results. Whether used in manufacturing, recycling, or maintenance, they are a key piece of equipment for preparing cables for further use.

C02 Engraving Machine
SG Laser's CO2 engraving machine utilizes a CO2 laser to create precise, high-quality engravings and etchings on a variety of materials such as wood, acrylic, glass, leather and fabric. By focusing the laser beam onto the surface of the material, it vaporizes the top layer, leaving a permanent mark. This process allows for intricate and detailed designs, patterns, logos, text, or images to be etched with exceptional accuracy.
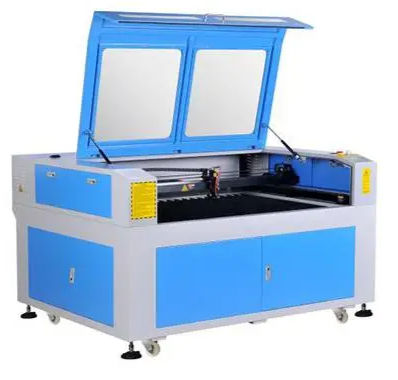
Engraving and Cutting Capabilities
-
These machines are usually controlled by specialized software, where you can design, import graphics (e.g., vector files), and control the engraving parameters (like speed and power).
-
Some common design file formats include .AI, .SVG, .DXF, and .BMP.
Control and Software
-
CO2 engraving machines come in different sizes, ranging from smaller desktop units to larger industrial machines capable of handling bigger workpieces.
-
The work area size will depend on the model, and larger machines can handle objects like signs, panels, or even furniture.
Work Area and Size
-
CO2 laser engravers can perform both engraving (shallow etching on the surface) and cutting (through-cutting thicker materials). The precision of the laser allows for high-quality, intricate designs and customizations.
-
The depth of engraving can be controlled by adjusting the power, speed, and focus of the laser.
Precision
-
CO2 engraving machines are highly precise, making them ideal for detailed logos, text, and intricate designs. This level of precision is crucial in applications like product branding, art, and custom gifts.
-
The engraver can control the resolution of the engraving to achieve fine details.
Integrated Cooling System
-
CO2 lasers typically have a cooling system (often water-cooled) to prevent the laser tube from overheating, ensuring consistent performance and longevity.
Materials Compatible
CO2 lasers work best on organic and non-metallic materials such as:
-
Wood (engraving, cutting)
-
Acrylic (engraving, cutting)
-
Leather (engraving, cutting)
-
Rubber (engraving, cutting)

High-Precision Cutting
Customization
Versatility
CNC ROUTER MACHINE
A router machine is a versatile, high-precision tool used in woodworking, plastic fabrication, and other industries. It is designed to hollow out (or "rout") areas in a workpiece, often for creating decorative edges, cutting grooves, shaping profiles, or making detailed cuts. Routers are commonly used for tasks such as edge profiling, carving, trimming, and shaping materials like wood, plastic, and even soft metals.
A highly automated router operated by a computer to perform precise, repetitive cutting tasks. CNC routers are programmed with software to follow specific patterns and designs.
Speed
-
Router machines, especially CNC versions, can achieve high precision and accuracy in cutting and shaping materials. CNC routers, in particular, allow for consistent results in large batches.
-
Routing tasks are completed quickly, especially with automated machines like CNC routers, which improve production efficiency.
-
Router bits are designed to produce smooth, clean cuts with minimal rough edges, which is especially important in fine woodworking and precision tasks.
-
Router machines can handle a wide range of materials, such as wood, plastic, composites, and metals (in certain applications). This makes them suitable for a broad range of industries.
-
Router machines allow for a high degree of customization, including custom shapes, designs, and profiles. CNC routers can follow complex, detailed patterns based on digital designs.
Smooth Finish
-
Applications: Used for large-scale production of intricate cuts in wood, plastic, composites. It's common in industries like furniture making, cabinetry, and signage.
-
Key Feature: The machine operates automatically, controlled by computer programming, allowing for high precision and efficiency in large production runs.
Advantages of Using Router Machines:
A router machine is an essential tool in many industries, particularly for tasks that involve shaping, cutting, trimming, and profiling materials. Whether handheld or part of an advanced CNC system, routers offer flexibility, precision, and speed. They are indispensable in woodworking, metalworking, and plastic fabrication, providing both professional and amateur users with the capability to create intricate designs and precise cuts.
Summary: